
Below are images of what a homeowner should ALWAYS expect for their money vs. sub-par workmanship.
Leak free workmanship
A roof systems primary function is to keep water from entering the house structure. This must always be the first goal in the installation process. When proper install practices are used, the workmanship will mirror the lifespan of the materials.
The right way
The wrong way
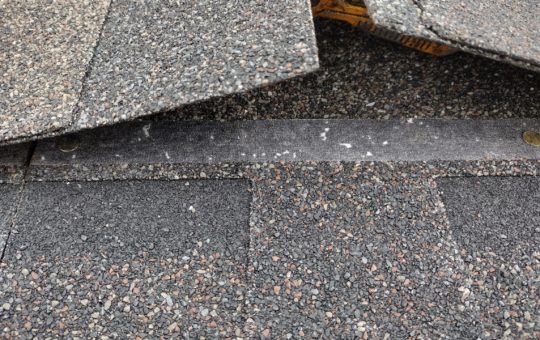
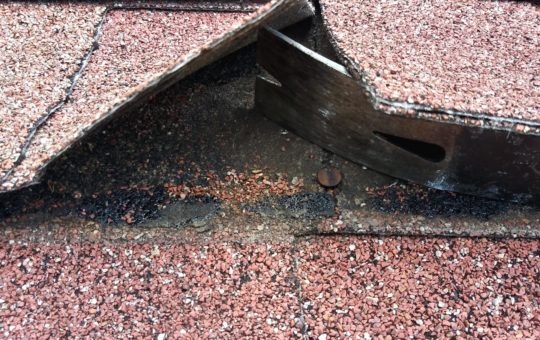
Butt joints with improperly placed nails are a common cause of leaks. A misplaced nail will usually not be an immediate problem but over time will develop into a leak that can be costly to the homeowner if it falls outside of the warranty period. Misplaced nails often require extensive searching (lifting of shingles) to be found. This in turn can cause more damage if the shingles will not easily separate. It is easy to see how a simple mistake could cause extensive damage to ceilings and the home interior before the leak is found.
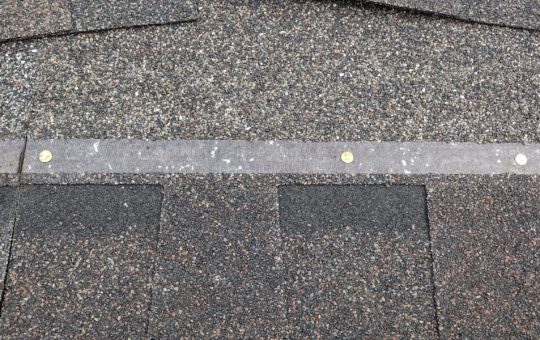
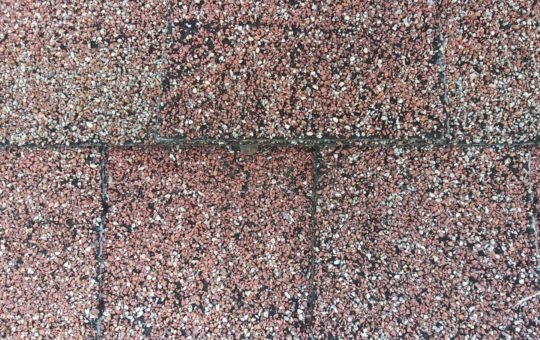
Low nails are another major cause of roof leaks. When proper care is not taken, nails can be shot too low and end up below the shingle overlap. This too will usually take time before a noticeable leak appears.
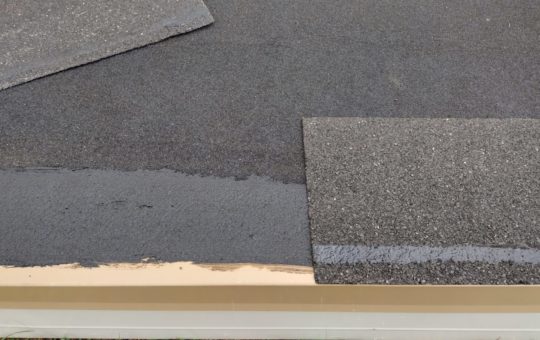
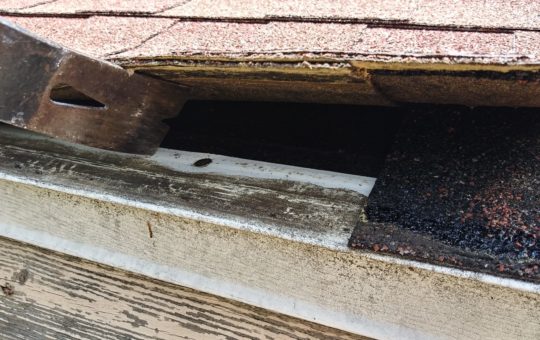
Sealing shingles around eaves, rakes and penetrations is another important procedure. Not only does it prevent water from penetrating the roof, properly cemented eave and rake shingles prevent damage due to lifting in high winds.
This image not only indicates the total absence of roof cement at the eave, but it also shows the lack of nails in the drip edge. This metal could easily be ripped off in a high wind situation causing a chain reaction with the shingles.
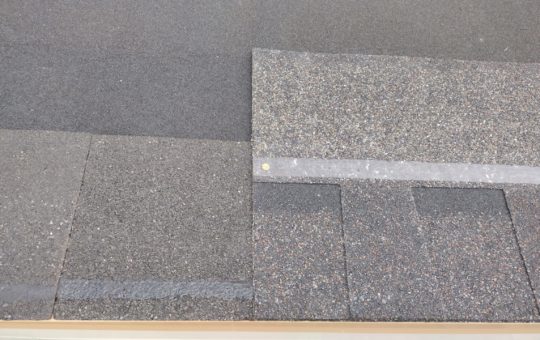
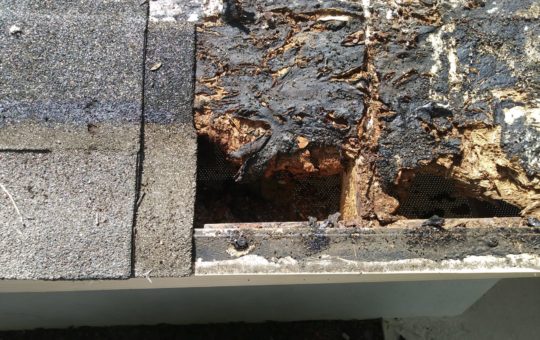
Starter strip overlap is another crucial detail that causes eave leaks over time. Offsets or steps in shingle installation are required to prevent double stacked butt joint leaks. this same offset is just as necessary for starter strips. If the offset is too little, water can find it’s way past the starter and penetrate the roof causing deck and structural wood damage. This offset is about an inch and a half. Clearly well under the necessary requirement.

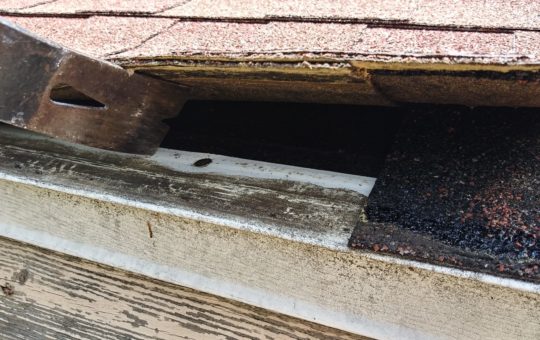
Nail spacing on the roof is critical for the prevention of leaks AND to ensure that it can withstand the high winds during storms. Code requires 4 to 6 inches on eave drip depending on the zone. Our standard practice is 4 inches.
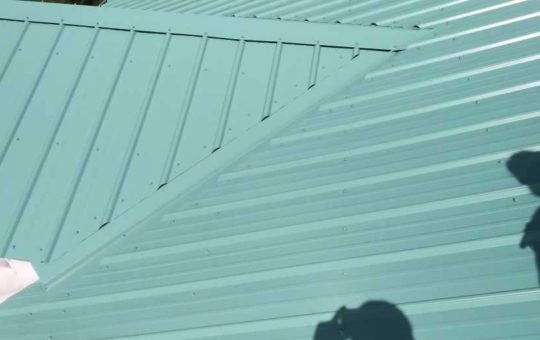
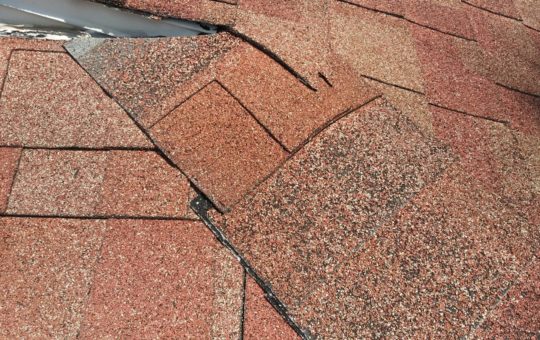
The number one cause of exposed fastener metal roof failure is improper screw installation. Overtightening of screws can lead to backing out and a screw that is not vertical to the panel may suffer rubber washer failure.
Attention to detail
It can’t be argued that the primary goal in roofing is to protect the home from water damage. However, the close second is a roofs look or appeal. Although the images below won’t cause leakage, aesthetically these homeowners are not getting their moneys worth.
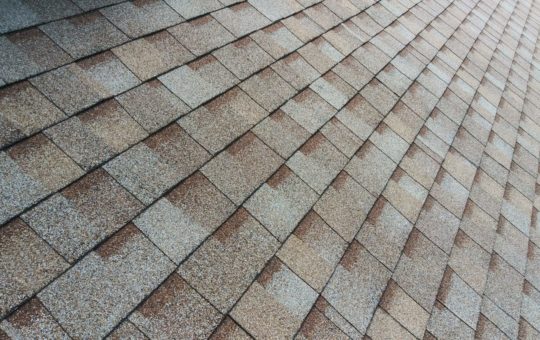
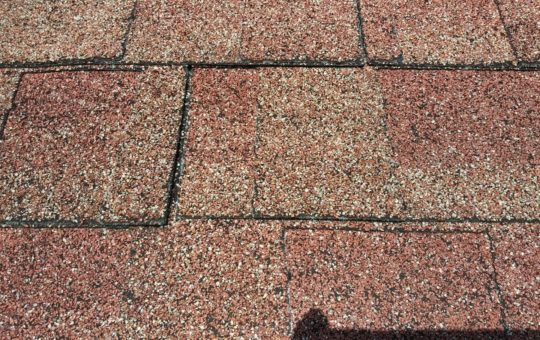
Perfect lines not only look great, they also ensure that nails are covered and adhesive strips adhere in the proper place.
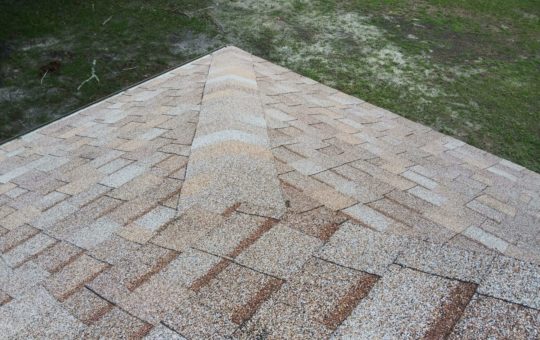
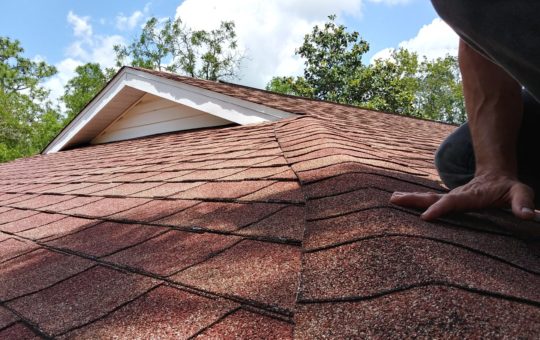
Snapping lines for cap and shingle alignment takes a bit more time but ensures lines stay straight.
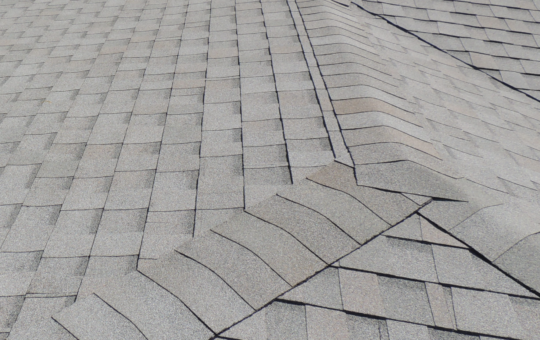
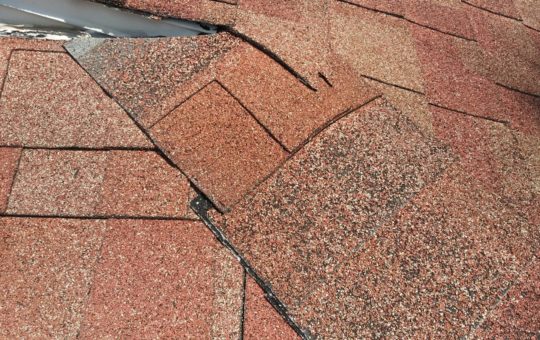
There are times where mistakes are made and material is short. In such cases it is a companies responsibility to get more material to finish the job correctly. When money or speed becomes the driving force, corners are cut that are unsightly.
More images of lackluster workmanship.
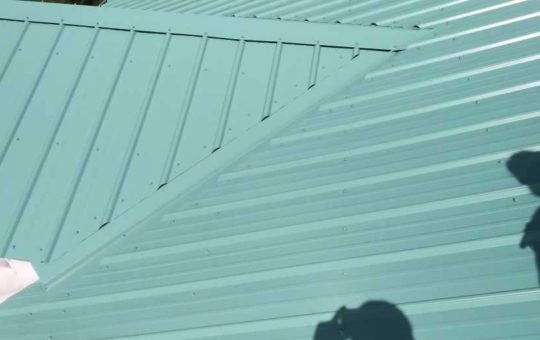
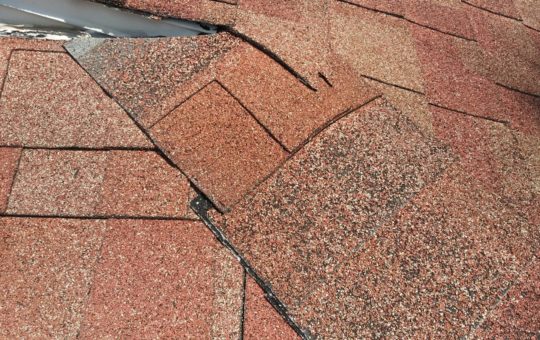
Metal roof systems have their own challenges. In this case properly cutting valley panels.
Straight cut valleys look clean and are preferred over “California cut” valleys. This method is also the least likely to cause build-up of debris.
Painted boots & vents not only look better by blending in with the roof color, they also tend to add another layer of protection to the vents prolonging their life and painted boots tend to deter squirrels from chewing the lead.
Properly spaced nails are the most important factor on a shingle roof. They prevent leaks from occurring while also ensuring that the shingles stay in place in high velocity wind storms.
Drip edge’s, vents and boots also require correct nailing to keep them in place during wind storms as well.
Cementing protrusions correctly prevents leakage. Layered cementing during installation adds another layer of protection and prevents potential tab lifting in storms.
Better materials give a cleaner more finished look and provide better protection.
